

It is quite obvious that you should first design a panel you want to apply. It is similar to baking a cake, but better! 2 mm aluminum sheet with signs of baking tests – the top decal was close to burning – it turned yellow, the left (red) one looks fine then I scrached them with nails and screwdrivers to see how durable they are You can do the same before you start seriously. Thats how I determined how the fixing (or preserving) the decal in the oven should look like. I’ve just printed my final panel design and some additional colourful strips I used for tests. I used old and trusted aluminum sheet to get the decal melting temperature. With a little experience the results can be veeeery good at least.īefore I made my first panel, I spend some time experimenting with waterslide decal I bought. One A4 sheet costs about 2 euros and can be purchased easily with online stores or auction sites. In this tutorial I used Forever Waterslide (non HT version), designed to work with laser printer. Lazertran decals seems better, but I wasn’t able to buy them in Poland (where I live). Forever Waterslide) – we have to take care of the appropriate print protection foil can be transparent or white – I use transparent as it is more versatile.
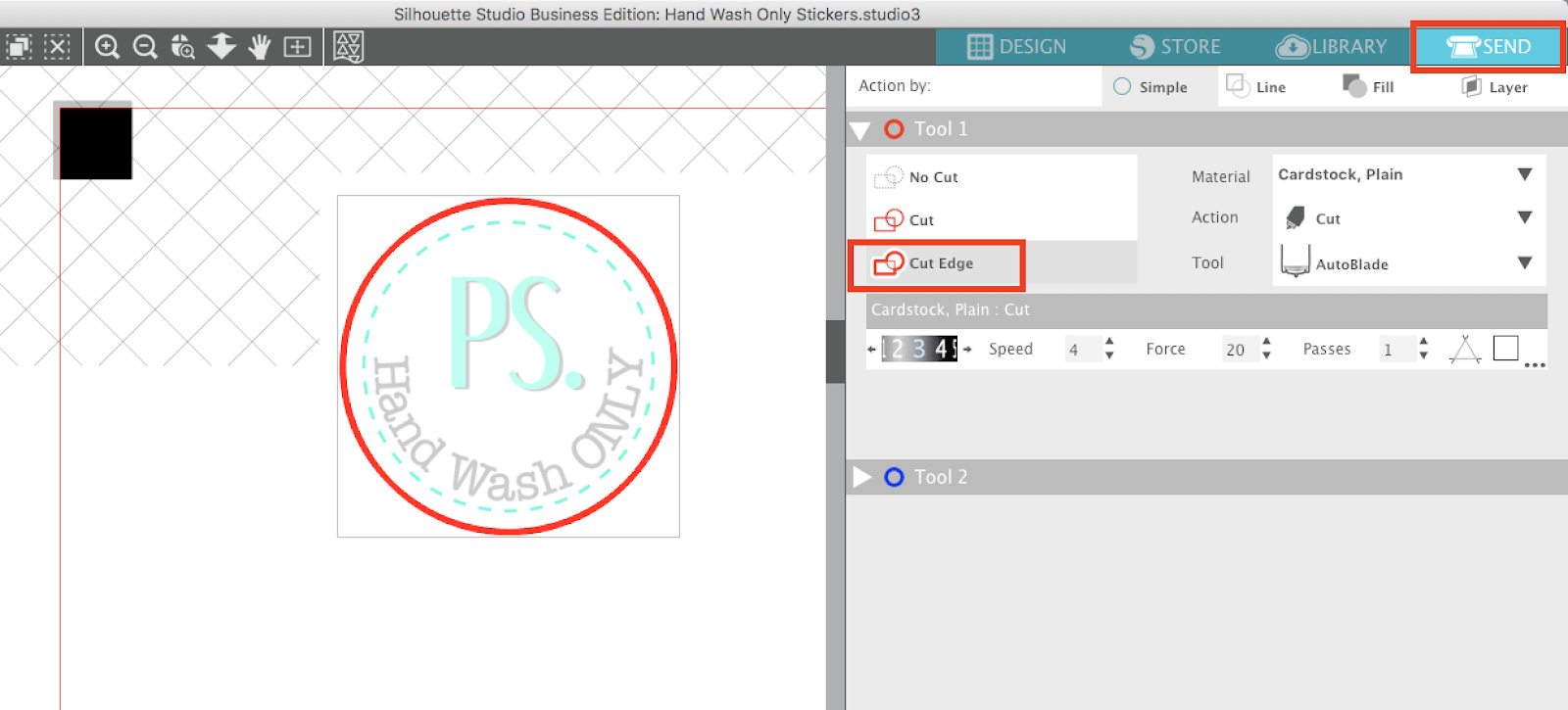

Waterslide decal is made up of backing paper and thin, but strong, foil. So, lets make our eurorack module more interesting by adding pots and jacks descriptions along with some decoration! The previous part was mostly about drilling the holes in aluminum sheets, quite boring stuff. This is a part 2 of my eurorack DIY module building tutorial and it describes how to apply graphics on your blank panel. For last 4 years I made around 35 eurorack DIY panels for different kind of devices using water decals. Some techniques described here may seem weird (or stupid), but all of them are based on my own experience.
